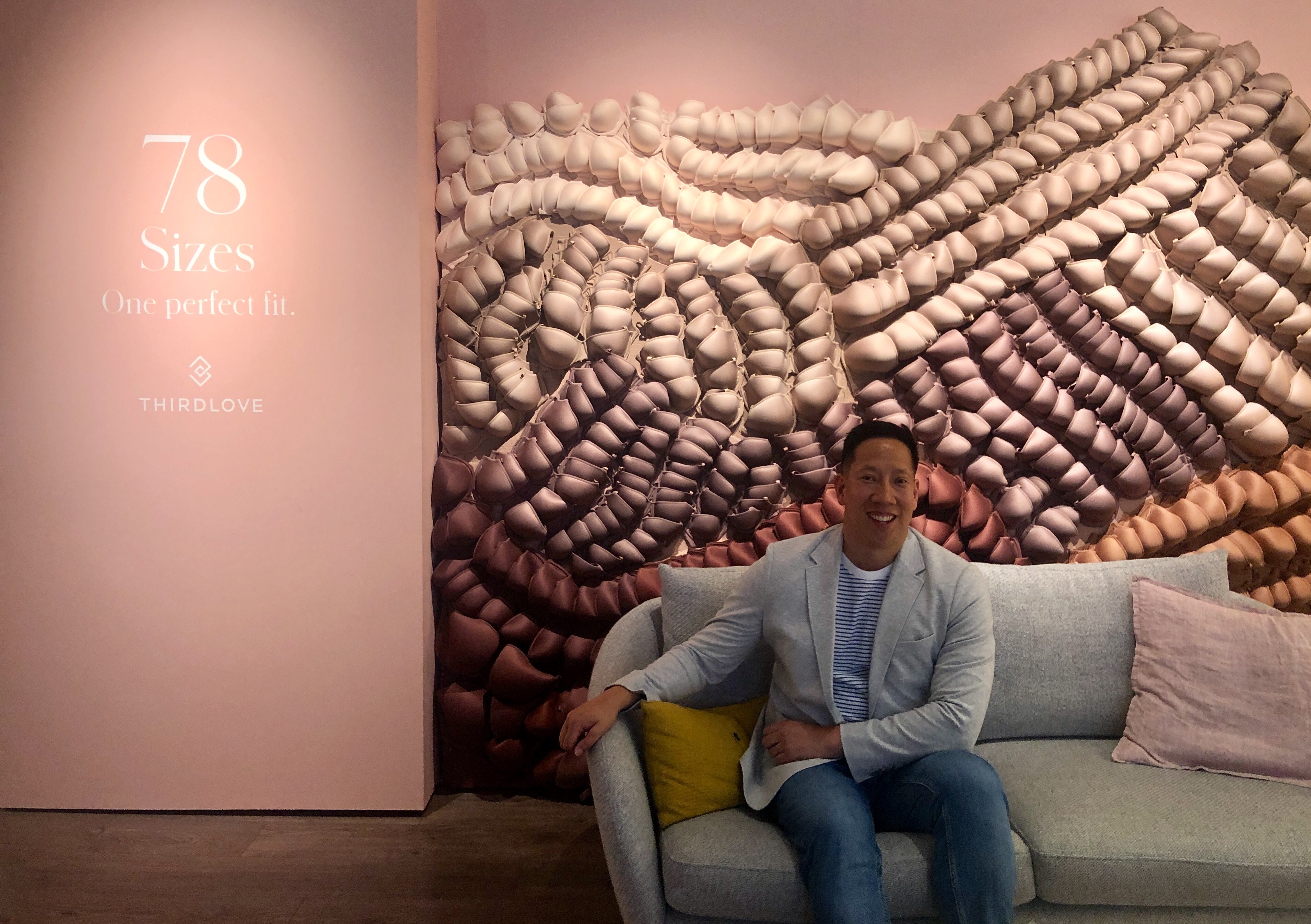
September 18, 2019
Vendor Relations & Social Responsibility: Marcus Chung of ThirdLove
Marcus’ Journey
Marcus’ career is interesting. He began at established apparel brands, such as Gap, before progressing to innovative start-ups, Stitch Fix and, currently, ThirdLove where he responsible for both sourcing and social responsibility.
“I really loved it.” Marcus says of his time at Gap. “It was my first exposure to the apparel industry and a great opportunity to be part of the social responsibility team which, at that time, was a leader in this space.” After Gap, Marcus moved to McKesson, a distributor of medical devices, before returning to apparel with Talbots. “It was an opportunity to take what I’d learned at Gap and start something fresh. I could think through, in a very different environment, how can we build a social compliance program from scratch? It was an area which was important for the company but we didn’t have the resources that Gap did. From there I followed my leader at Talbots, the Chief Supply Chain Officer, and transitioned to The Children’s Place where I was able to evolve its social responsibility program.”
“All through this journey I was lucky to work with someone who gave me the opportunity and insight into different parts of sourcing and the supply chain. I realized I was really interested in more of the operational parts of sourcing in addition to the social responsibility piece. I wanted to take greater ownership of the whole supply chain so I could execute with integrity and responsibility.
An opportunity then arose at Stitch Fix where I led sourcing for the private label business and, as a side project, I started its responsible sourcing program which blossomed into its own team. From there I moved to ThirdLove where, again I am not in a role focused on social impact, but I’m taking the same approach of starting responsible sourcing efforts.”
The Interaction of Vendor Relationships and Social Responsibility
Marcus has rare expertise in both social responsibility and product sourcing giving him a nuanced understanding of their interplay. “Placing orders with factories which don’t have enough capacity or changing elements of the product, but not extending deadlines, drives up working hours. The first thing I do now is get a sense of who we are working with. Who else is in those factories and what percentage of their capacity we take up?” Sourcing strategy is key here, says Marcus. “To build those relationships it is much easier if you are working directly, working FOB. You start with a much greater need for transparency than if you have agents in the middle or via LDP.”
Marcus’ approach to factory transparency over working hours and benefits is instructive of his experience. “At a large company, we could say to our vendors you must open up your records and there will be consequences if we find double books. This was possible because of their scale and because of redundancy in their supply chains. Knowing that if they lose one factory there are plenty of others which can pick up that type of production.
It’s much harder when you are at a small company, especially if you are growing and scrambling to get vendors to work with you,” says Marcus. “You need to figure out what benefits you bring to the vendors and really try to emphasize that to the factory. At ThirdLove and Stitch Fix, where we were not as significant to the vendors from a volume perspective, they saw us as the future of the industry – and that becomes your value proposition instead of large orders.”
“It’s about transparency and continuous improvement,” says Marcus. “In sectors where social responsibility isn’t as mature, jewelry for example, you will find more non-compliances but its really up to the brands to figure out how to engage with the factory. It’s incremental change. You aren’t going to change factories overnight. It’s a baseline of what you can tolerate and what you can’t, but there are shades of gray. As long as there aren’t those really egregious violations, it’s then up to the company to determine if it believes it can drive improvement and can they tolerate the pace of change.”
Should Social Responsibility Be Independent from Sourcing?
Having worked under both arrangements, does Marcus believe social responsibility functions best when independent from product sourcing, or, instead, within a combined business unit having shared accountabilities? “I’ve found keeping the reporting in the same space is more powerful,” says Marcus, “but it’s really hard to make decisions. The bias, especially at smaller, dynamic companies, is to enable sourcing and production because they need the product. I have to check myself. How do I balance the short-term benefits vs the long-term risk?”
“At Gap,” says Marcus, “the two functions were entirely separate to avoid conflicts of interest so that whatever recommendations the social responsibility team made were completely uninformed by sourcing strategy. There is value to that approach. However, when I was reporting to the chief supply chain officer, I found that the connection point with sourcing and production was so valuable to make change happen. It helps the CSR team prioritize and anticipate where the risks in the supply chain will come from. Also, having the sourcing director in the conversation with factories enabled us to speak to common goals. You can pass information off to the sourcing team and ask them to address it. However, that’s not going to take as much importance as costing or quality, for example. The sourcing director doesn’t feel one hundred percent comfortable speaking and the person they are speaking to similarly does not understand. But if you have sourcing and social responsibility represented usually what happens on the factory side is the HR or sustainability manager will be present as well. It gives it a level of importance when you speak together and starts to have more impact.”