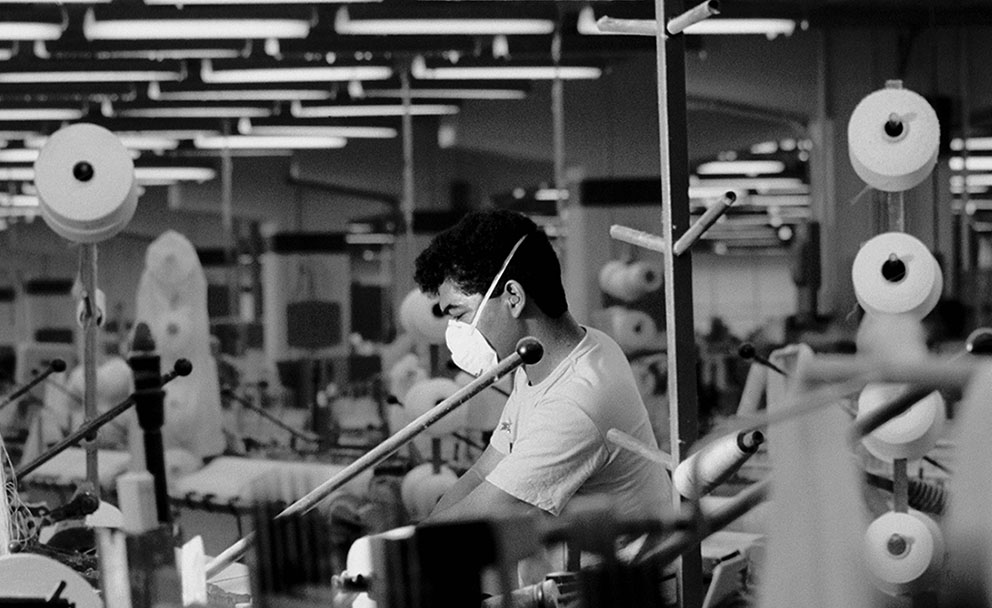
With the Lunar New Year approaching, attention in the responsible sourcing community turns to China where millions return to their homes for the festive period making this the largest annual migration of humans on earth. Production usually grinds to a halt during this period and chaos can often ensue as many workers choose not to return after their holiday taking up opportunities closer to home. Factories can lose 30-50% of their workforce after Chinese New Year with major implications on the workplace conditions their remaining workforce is subject to. What is the current situation in China? What strategies are suppliers employing to minimize impact and how significant a challenge shall this be in the future?
While the problem of worker retention is at its most acute after Chinese New Year, the plates have been shifting in China for some time. The Chinese low cost labor force is more nimble than ever. No longer do young Chinese citizens aspire to work in manufacturing but, instead, aspire to more prosperous futures than those of their parents. Chinese suppliers in the coastal regions are struggling more than ever to retain workers. Government initiatives to transfer low cost manufacturing out of the Guangdong region, for example, has led to a wealth of new opportunities in the inland provinces where the costs of living are significantly lower and workers have the opportunity to reside closer to their families or even at home.
The most common strategy suppliers employ is incentivizing their workforce to return with a system of bonuses. Some suppliers, for example, will offer RMB15 per hour, rather than the usual RMB10, for 5 days after Chinese New Year. In the Shanghai region, it is common for there to be a loyalty bonus which is accrued over the year but only paid after the holiday. In the Guangdong region most factories entice their workers to return in the form of a red pocket (开工利是) in the region of RMB200 – RMB500.
In an industry with notoriously thin operating margins, there is debate as to how financially sustainable these practices are. The challenges are systemic and fundamental. As such, forward thinking suppliers are more commonly adopting a holistic approach. One of the major causes of low retention rates, estimated at 70-80% in China, is that workers have migrated great distances with the accompanying challenges of displacement and homesickness common. Suppliers then are making efforts to develop a sense of ‘family’ within the workplace emphasizing better interpersonal relationships. Child care is more commonly provided now, with qualified care workers, and double rooms for married couples. Reduced dormitory fees and free of charge, or lower cost, health care is also more readily available. There is a greater focus on improving worker relations via dispute resolution and management services, worker assistance plans, worker satisfaction surveys and, increasingly, worker voice.
Over the medium to longer term the challenge posed by worker retention is becoming less pronounced anyhow. The demand for low cost manufacturing labor is declining in China. This is due to declining demand from Europe and The United States, increasing labor costs, greater competition from other markets, the ongoing consolidation of factories and, importantly, the growing trend towards better mechanization and automation within the Chinese manufacturing sector.