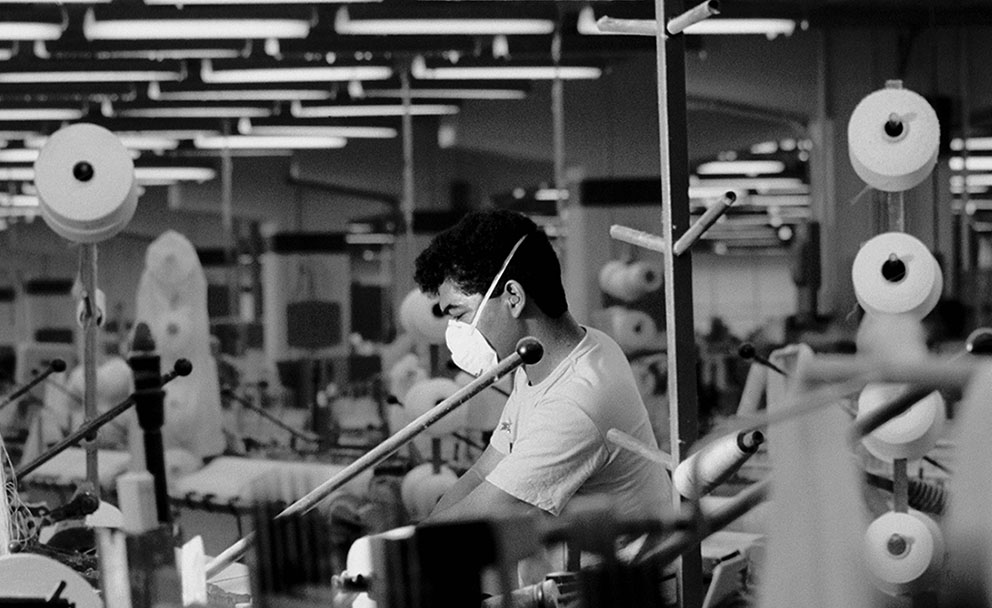
The rise of China as a manufacturing hub has been inexorable. In 1990 China produced less than 3% of global manufacturing output; its share now is approximately a quarter. The dynamics though are changing. Since 2001, manufacturing wages have risen by an average of 12%, annually, and its worker age peaked in 2012. Further, internal migration is slowing down as workers are unprepared to accept the drudgery their parents once did and a recent series of strikes demonstrate that its labor force is becoming more disaffected. Despite China’s inherent strengths, including excellent transport links, deep sea ports and excellent productivity, it cannot maintain its position forever, even if it wanted to.
Faced with this outlook, suppliers are looking for solutions. One option is moving production into the hinterland where land is cheap, tax breaks available and its large pool of lower cost labor is, importantly, local, allowing factories to quickly restart production after Chinese New Year. A second option is offshoring production into neighboring South East Asian countries with more favorable demographics and where average wages are lower, up to 3 to 4 times, in Vietnam and Indonesia, for example. This process has, in fact, already begun in the garment sector due to its low cost, low skill and highly transportable nature. Cambodia and Myanmar have become notable beneficiaries as Chinese suppliers increasingly establish production there.
Despite these advantages, relocating production is highly disruptive, very costly and at significant risk. Factories are also discovering that the logistics networks, which they depend upon, are far less reliable in the hinterlands than those on the coasts. Consequently, Chinese suppliers are also turning to a third option of employing trafficked labor from Laos, Myanmar and, most significantly, Vietnam.
Attracted by the opportunity to lower overheads and increase flexibility, without the need to relocate production, factories in China are increasingly tempted to work with labor traffickers. Working directly with the factories, these organizations recruit workers, move them across borders, issue forged national IDs, provide coaching and, in compensation, deduct approximately RMB500 (USD80) per month from salaries creating a form of bonded labor. Drawn by the opportunity to earn two or three times their current salary, Vietnamese workers are incentivized to the extent that Reuters estimates that the number of illegal Vietnamese migrants rose 20% in 2015 to 107,000. Just last month border guards at Thai Binh Province in Vietnam stopped a bus carrying 32 workers and arrested a local woman for allegedly attempting to smuggle them into China.
The issue of trafficked labor in China remains, for time being, on the margins of the Chinese manufacturing industry. Omega is of the view though that it will become more common as cost pressures increase and the dynamics of the region evolve. It goes without saying then that this has important consequences for responsible sourcing programs.
It is important that brands and retailers have a clear understanding of how their supply chains are exposed to forced labor and have procedures to identify and remediate issues. Identifying and remediating forced labor is a complex issue. For more information, please contact us.