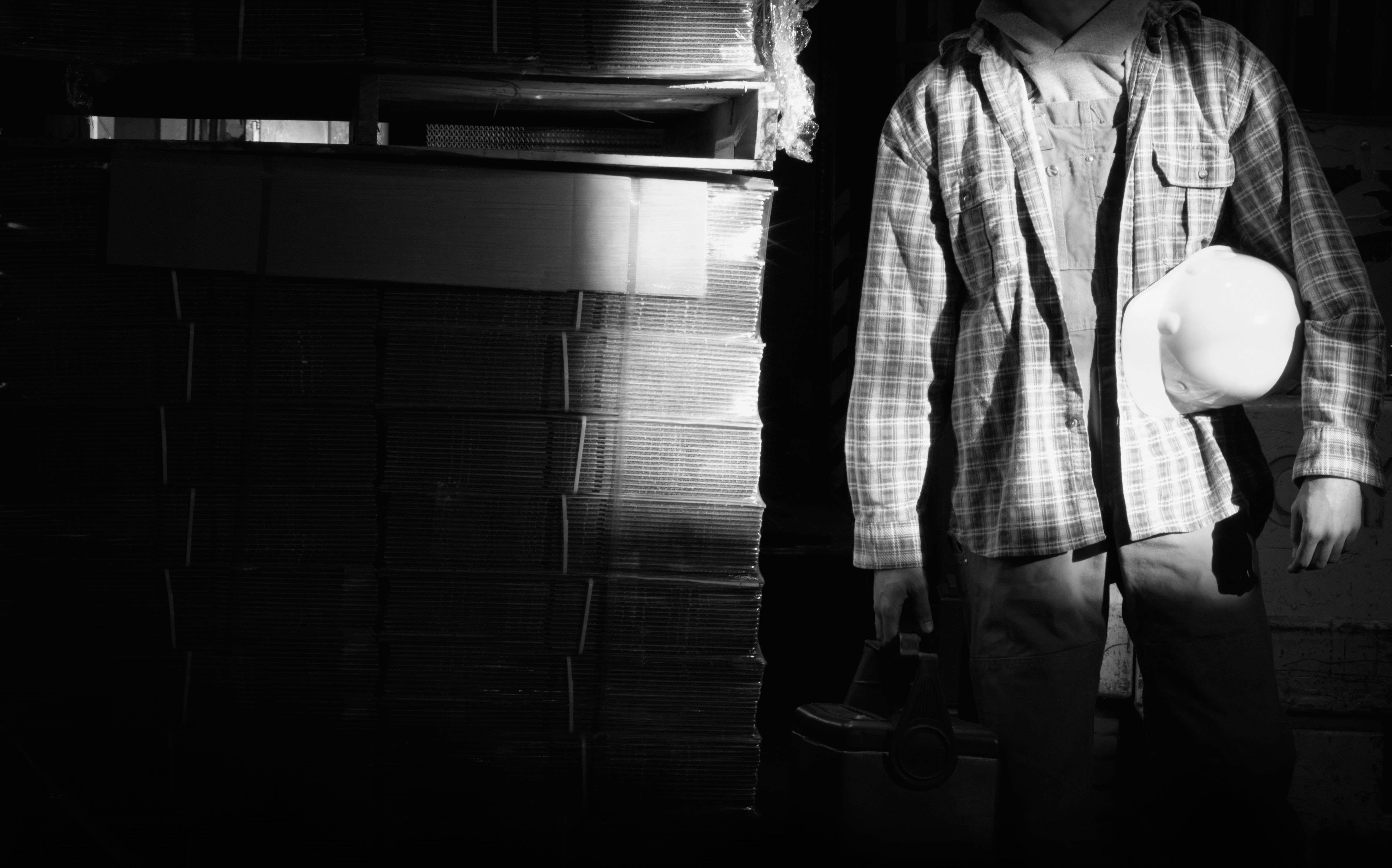
A worst case scenario for any company is learning, either through the media or other sources that, not only are their products manufactured at factories with egregious workplace violations, but they were unaware that they were doing business with these manufacturers in the first place.
Supply chain transparency is not as simple as it may seem. In many cases the party with whom a company places its purchase order is little more than a sales office in New York, a vendor showroom in Taiwan or a shell company in Hong Kong with actual production occurring at an unnamed manufacturer, usually overseas, with whom it has only a tenuous business relationship.
Supply chains are inherently murky. While the problem is less acute across apparel and footwear suppliers, more vertically integrated and benefitting from consistent business relationships, the issue is prevalent and a real challenge for companies looking to develop an effective program from the ground up. For companies to have a real understanding of the working conditions on the ground it is essential then that they dig beyond this first layer.
The only way to understand where your product is made is by demanding the information from your suppliers. However, in fear of being cut out of future transactions, suppliers are often reluctant to disclose these details. As such, buying relationships will need to be leveraged, with full disclosure a condition of business. Even then supply chain mapping can take months to complete.
Once a company has mapped their Tier I suppliers, it is important to consider the real possibility that their products are actually being manufactured elsewhere, further upstream in the supply chain. Subcontracting poses a real challenge to brands with the issue falling into two general categories.
The first category is where a manufacturer subcontracts a process, or several processes, to a third party, or third parties. In the case of a toy umbrella, for example, the vendor may declare the manufacturing site to be where the product is shipped from. However, this may be a simple assembly room with the fabric manufactured at factory A, the wooden handle at factory B and the spokes at factory C. Another example would be a basket facility in Indonesia or The Philippines for example. In this case the site, declared by the supplier, may be a simple packing room with the main production process subcontracted to homeworkers with the requisite skills for the creative, indigenous designs required by the buyer. This scenario is commonplace in India also where apparel manufacturers sometimes outsource delicate embroidery to workers based at their homes or in small, poorly regulated workshops.
The second scenario is where a factory accepts an order from a buyer but, due to capacity issues, or wanting to increase its margin, the factory subcontracts the entire order, or part of the order to a separate manufacturer without requesting permission from the client. This practice is not uncommon across the industry. In fact, it was thrown into sharp focus by the Rana Plaza tragedy in Bangladesh. Here, due to undisclosed subcontracting, a number of companies were unaware that their products were being manufactured at one of the many factories operating within the building.
Given these challenges then what should companies do? First and foremost, it is crucial that you understand where your Tier I factories are. While this is often an exhaustive exercise, once complete, and baseline audits performed at these sites, you have a clearer picture of your supply chain locations as well as conditions on the ground. With this information brands can then begin to understand where the risks are and dig deeper to learn whether subcontracting, and what types of subcontracting, is occurring. This can be achieved through by requiring factories to declare details of their subcontractors / Tier II factories. Subcontracting can also be detected through quality inspections, or onsite audits, where auditors form a judgment based on, among other examples, production capacity, types of machines or the contents of the raw material storage.
If unauthorized subcontracting is identified in a supply chain a decision needs to be made. If a factory is subcontracting entire orders then the brand may choose to disqualify it from future business. However, if the factory is openly subcontracting a process, such as the weaving of wicker baskets to homeworkers, then the brand may consider accepting this supply chain partner and perform an audit upon that site to assess its workplace conditions. However, the brands may wish to tailor the assessment since it will be performed upon a residence as opposed to a manufacturing site. While there remains some debate on the best way to manage subcontracting, the industry has made significant progress over the past 5 years and a number of leading brands have now built audits of Tier II suppliers into their core programs.
Omega has vast experience in supply chain mapping and managing compliance programs across subcontractors. Should you require information on our services do please contact us.